From the first generation RS 6 to the current one: Stephan Reil was there from the start and had a lot of influence on the development of the high-performance Audi. A graduate engineer, he became Division Head for Vehicle Customization at quattro GmbH (now Audi Sport GmbH) in 1996. In 1998, he took over as Head of Vehicle Development for all of the company’s complete vehicles and since 2020 he has been in charge of technical development for AUDI AG at the Neckarsulm site. On the twentieth anniversary of the first generation RS 6, the C5, Reil looks back on the challenges in development and technical refinement and remembers defining events.
Mr. Reil, when did development start on the C5 (2002-2004), the first generation RS 6?
The Audi RS program originally started in the mid-range. In 1999, we had just started in the market with the Audi RS4 Avant (series B5) when the question arose: What could the rest of the portfolio look like? The RS 6 in the C-segment – the luxury class – was the next logical step. The result was that after developing the RS4, we concentrated fully on the RS 6 project.
What does the first generation represent for you personally?
Primitive achievement!Its biturbo V8 with 450 PS stands out for its superior performance. In terms of power, we wanted that to immediately create a significant difference from the S model in the A6 series and the competition. And we did that! When the RS 6 made its debut at the Geneva International Motor Show in the spring of 2002, its 450 PS put it at the top of the segment. But on the other hand, that car was supposed to be a wolf in sheep’s clothing that would win people over through understatement. I remember a quote from Auto Motor und Sport. It said,“It’s not ostentatious” and it has “as good as zero” stage presence. So our plan was working.
When there is supposed to be that much performance even in everyday use, how do you test that?
In the early phase of each RS model, we drive one of the first prototypes about 8,000 kilometers (4,970 miles) on the Nordschleife of the Nürburgring over about three weeks. Then, shortly before that particular model is presented to the world, we do that 8,000 kilometers again with a pre-series vehicle as part of the release. What’s noteworthy about that is that the Nordschleife makes demands on a wide variety of components in very different ways. There are real difficulties in each individual meter, like the compression in the Fuchsröhre section, the vibrations in the Caracciola-Karussell, or the jump at the Pflanzgarten. So one kilometer on the Ring is like as many as 15 kilometers of normal, everyday use. There are also extensive winter tests in Sweden and Finland. The same also happens in hotter regions, like in South Africa or Death Valley. We can also simulate these kinds of constraints in our climatic wind tunnel. Then there are also high-speed drives, which we do on the testing ground in Nardó, Italy, and mountain driving, including on the Grossglockner in Austria. The prototypes are on the road almost everywhere in the world!
Appropriately, the RS 6 made its market debut at the Nürburgring.
Yeah, we wanted to give the RS 6 an aura of motorsports from the outset, so for its maiden voyage, 30 Audi dealers competed in their demonstration cars on a corso on the Nordschleife as part of the 24-hour race on the Nürburgring in front of 194,000 spectators. It was really an impressive scene! And apropos of motorsports, in North America, where the C5 was only available as a sedan, it was used specifically for racing in the Speed GT class as part of the American Le Man Series (ALMS) program. Within 15 weeks, the Champion Racing team built the racing version, the RS 6 Competition, with our support. The competition car weighed 1,383 kilograms (3,049 lbs.) and its biturbo V8 had 475 PS.It used a manual six-gear transmission from the Audi S4. Randy Pobst was the champion right in the first season. His teammate Michael Galati came in second. It was a massive success that impressively documented the potential of the biturbo V8 concept in conjunction with all-wheel drive.
Give us a picture of what series production of the first RS 6 C5 looked like.
About 80 percent of the first RS 6 was built on the regular A6 production line. But the parts that were developed specifically for the RS 6 – the skirts, sill extensions, or for instance the intercooler for the V8 – had to be produced in a special, complex process. So the cars were still incomplete when they were taken from the series production line to the quattro GmbH halls, where we completed the precision handwork on the hydraulic lift over about 15 hours. The technicians installed the intercoolers first, then the intake system, and then the skirts and sills. And then finally the wheels, which were too wide for the regular assembly line. We were able to finish about 20 cars a day like that.
Let’s turn to the second generation of the RS 6 C6 (2008-2010). Ten cylinders, two turbochargers, 580 PS: at the time, it was the most powerful Audi of all!
With the C6, we were exploring the limits of what was technically possible at the time. Its five-liter V10 is the biggest RS engine ever built and we constructed the ten-cylinder’s biturbo setup specifically for the RS 6. So in all, there were three V10 variants at Audi. One variant drove the big sedans, the S6 and S8, and another was for the R8 supercar and the Lamborghini Gallardo. We created the most powerful new developments and the only one with turbochargers in the RS 6. We also integrated dry sump lubrication that we borrowed from racing, which steadily gave the engine more oil during moments of high lateral acceleration. With its two turbochargers and manifolds, the V10 already looks like a work of art. And it’s powerful. I don’t know of any engine compartment that is filled better than the one in the RS 6 C6.
From the philosophy of the massive V10 drive system in the C6 to downsizing the C7 (2013-2018) to a V8: how did that come about?
In a certain way, the greatest strength of the C6 was also its greatest weakness. The enormous, heavy engine sat largely in front of the front axle. On a straightaway, it is almost uncatchable. But the downside of its axle load distribution becomes apparent on tight curves. So when we were developing the third generation of the RS 6, we focused on better lateral dynamics. We wanted to make the C7 more agile and we urgently wanted to take off weight, particularly from the front axle. One benefit was that all the components are made of aluminum in the base-model A6, which was based on the modular longitudinal matrix (MLB), which was new at the time. The engine in the MLB is also further back in the car. That, combined with the lighter V8 engine in the new RS 6 of the C7 generation, distributed the axle load much better. So despite having 20 PS less than its predecessor, that car is faster, sportier, and, thanks to cylinder deactivation, more economical than the C6 in every way. The C7 was a huge leap forward for us, particularly in terms of driving dynamics. Thanks to the improved weight distribution, the RS 6 was now able to hug the curves and, thanks to launch control and a rapid-shifting eight-gear automatic, the C7 raced to 100 km/h (62 mph) in 3.9 seconds, which is a good half second faster than its predecessor.
The DRC chassis is still being used in the RS 6 to this day. What is its benefit?
The DRC (Dynamic Ride Control) chassis is part of the DNA of the RS 6 and was completely redeveloped at the time specifically for the C5. Its construction with dampers linked diagonally via oil pipes reduces roll and pitch movements during dynamic driving. Since the C5 it has matured into a constant in RS 6 history. It combines proper comfort with taut driving dynamics. DRC technology has been in development continuously. Since the C6, it has been combined with adjustable dampers and it’s also available in today’s C8 upon request. Starting with the C7 generation, we also offer adaptive air suspension as a standard feature. Of course, for the RS 6, it has a sporty application with 20 mm (0.79 in.) lower ride and a binding setup that is still good for everyday use.
Let’s talk about the current generation RS 6 , the C8. The seemingly eccentric C8 appears to have only a little bit in common with the former “wolf in sheep’s clothing,” don’t you think?
Yes, that’s true.With the C8 generation, the RS 6 outwardly makes a clear contrast with the base model. For instance, we’ve widened the wheel arches by four centimeters (1.6 in.) each, the oval tailpipe trim is 33 percent bigger than its predecessor, and the rim diameter has grown by up to 22 percent with the option. Incidentally, its flat Matrix LED Headlights come from the RS 7 . In order to make that possible, we have also implemented an independent hood for the RS 6. In all, the RS 6 of the C8 generation only takes three outer skin components from the base model A6 Avant. All other exterior components have been changed and are RS-specific.Depending on the customer’s needs, it’s possible to decide whether an RS 6 should be more or less of an understatement based on numerous exterior and interior equipment variants and visual as well as design packages. This changeability, coupled with a high degree of everyday usability, is another important element of the RS 6 DNA. The C8 is also the first RS 6 to come as a 48 volt mild hybrid. A belt alternator starter (BAS) replaces the alternator. It has an additional electrical system with 48 volts and its own battery. While coasting or braking, it generates more energy than a conventional generator. In every other situation, it puts less strain on the engine. When it made its world premiere, the RS 6 was the first and only mild hybrid technology in its segment. With the current C8 generation, the RS 6 is also available as an Avant in North America for the first time. So it has grown into a worldwide success story on many levels. For me, it’s the crowning achievement of two decades of RS history.
Stephan Reil was born in 1965 and studied mechanical engineering and automotive engineering in Wiesbaden. He began his career at Audi AG in 1990 and became Division Head for Vehicle Customization at quattro GmbH (now Audi Sport GmbH) in 1996. From 1998 to 2001, Reil was Head of Development and Production, and, from 2001 to 2017, he was responsible for all complete vehicle projects and equipment features of Audi Sport GmbH. From 2019, he supervised the reorientation of the Technical Development unit. Subsequently, Reil assumed the position of Chief Operation Officer (COO) of Technical Development in Neckarsulm. Since July 2020, Stephan Reil has been Head of Audi AG’s Technical Development unit in Neckarsulm.
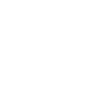